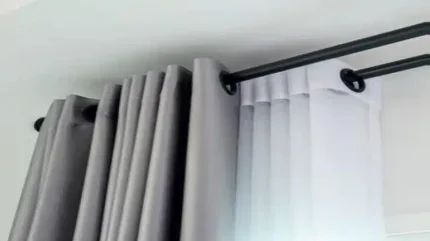
The ingenuity of manufacturers in devising a bewildering variety of items to attach to textiles is amazing and it will be obvious to cleaners that in many cases little, if any, thought has been given as to how they might respond to dry/wetcleaning processes. In terms of buttons alone, the huge and constantly changing variety of design and construction means that, particularly in the case of designer items, if buttons, buckles and so on are lost or damaged, the cleaner may find it impossible to obtain replacements to satisfy the customer. As many will know to their cost, the loss of a button or damage to just one item from a designer garment can lead to huge frustration trying to find a replacement that is acceptable to the customer, to say nothing of the cost if they decide to go to litigation!
Responsibility
It is not unusual to find disclaimers displayed on some cleaners’ premises stating that they do not accept responsibility for damage to – or loss of – buttons, buckles or trims. Such notices would appear to deny customers their rights under the Consumer Rights Act 2015. A cleaner supplying services to the public must meet the following standards under this Act:
- The service must be carried out with reasonable care and skill.
- Information said or written to the customer may be binding where the customer relies on it.
- The cost of the service should be reasonable.
- The service should be carried out within a reasonable time.
Therefore, the cleaner cannot deny all customers, across the board, one of their basic rights under the Act (to have their items cleaned with reasonable care and skill). If, at reception, a problem is foreseen with buttons trims et al on a particular item, the cleaner should bring this to the attention of the customer and either reject the item, protect it, or process it at ‘owner’s risk’ for this specific hazard. Alternatively, an additional charge might be made for removal and replacement of the suspect trim. Although the international standard1 for drycleaning requires that buttons, trims, beading and stitching must be able to withstand the cleaning process specified by the care label, it does not recognise any need for protection, such as covering buttons. However, if the cleaner sees at reception there is a risk of damage, he has a duty of care to tell the customer. Failure to do so may result in the cleaner having to accept responsibility for damage to buttons, belts, buckles and trims, if items are accepted without qualification, irrespective of any disclaimer notice.
Buttons and buckles
The loss of an odd button on many runof- the-mill items, such as men’s suits, does not usually present a problem, as they can easily be replaced. This is not the case with many ladies’ garments where there is an almost infinite variation in style and design. In the case of designer items, great care must be taken to prevent loss or damage and perhaps a major claim.
The cleaner has several options with buttons and buckles, which for the most part can be protected by covering them with metal foil. Alternatively, there are very effective specialist products available, which deliver a high level of protection.
Button damage spoils designer coat
Fault: following drycleaning in perc, the buttons on this high-value designer coat, which carried a care label, were found to be marked or chipped and the button in the photo showed obvious damage.
Technical cause: while the buttons were not considered to be delicate, cleaning in perc imposes very high levels of mechanical action and occasionally this results in damage, which in this case caused a major problem for the cleaner.
Responsibility: every cleaner should be aware of the many problems that can arise when cleaning designer garments and buttons are always high risk. Bearing this in mind, at the very least the cleaner should have taken the simple precaution of protecting the buttons.
Had this been done, the damage seen here could have been avoided. In this case, the cleaner failed in his duty of care and might have to take responsibility for the damage to the buttons.
Rectification: it is suggested that the cleaner negotiates with the customer and if possible, replaces the buttons.
Buckle leather curls and frays
Fault: the buckle of this belt, on a high value designer item, was covered in fine leather. The coat was labelled but was cleaned in perc (with the belt) on a Normal Cycle. The corners of the buckle frayed during cleaning and the thin leather started to peel back.
Technical cause: because of the fragile nature of the leather, it was not able to withstand the mechanical and solvent action during cleaning on a Normal Cycle.
Responsibility: in this case the responsibility rests with the cleaner who should have recognised the fragility of the buckle and brought it to the attention of the customer (or removed or protected it before cleaning). It is just possible that if a Reduced Cycle had been used, as dictated by the care label, the damage would have been avoided.
Rectification: it is possible the damaged buckle could be replaced with one of similar quality and colour and this would be the best solution.
Advice on a Reader Query. Black Eyelets – Even functional trim can fail dramatically in cleaning
Item: curtains fitted with black plastic eyelets to enable hanging on a round curtain pole.
Problem: widespread black mark-off became visible after drycleaning in perc solvent, with an apparent pattern to the mark-off which matched the circular eyelets.
Comments
1. We have seen this type of problem several times in the last 30 years.
2. It is usually caused by the surface of the eyelets being affected by perc solvent, which would make the curtains non-drycleanable in accordance with the normal care label symbol for curtains.
3. Perc is usually regarded as the solvent of choice for curtain cleaning (because of its superb cleaning power) and it is mentioned specifically in the British Standard for curtain fabric1 as the solvent used for testing for drycleanability. The problem here is probably the eyelets, not the fabric. 4. It is understood that the Court is going to reconsider the owner’s claim very shortly and the owner of the curtains has been asked to submit photos of the damage, with copies sent to the cleaner.
5. It might be helpful to establish whether the eyelets are in fact drycleanable. If one damaged curtain with eyelets could be available in Court, then (with the permission of the Judge) it could be checked as follows:
• The cleaner should bring to Court a very small container of distilled (preferably new) perc and a small pad of white cotton wool.
• Put on plastic gloves, then thoroughly moisten the cotton wool with perc and place it on one of the eyelets.
• Wait for 30 seconds or so, then use the pad of cotton wool to lightly rub the area where the pad has been sitting.
• Examine the cotton wool. If there is any black mark-off, then the eyelets and hence the curtains, should be deemed non-drycleanable in accordance with the normal symbol for curtain cleaning.
6. If the case were to be adjourned again, then there could be time for a simple British Standard test to be carried out by a commercial laboratory. The method to be requested should be according to the British Standard 41622. This is actually for assessing the resistance to drycleaning solvent of a button, but it is equally valid for a curtain eyelet.
7. Unfortunately, the judge may rule that the cleaner being the expert, the problem should have been foreseen and find for the customer.
We trust that these comments and suggestions are helpful in resolving this issue quickly and at minimum cost.