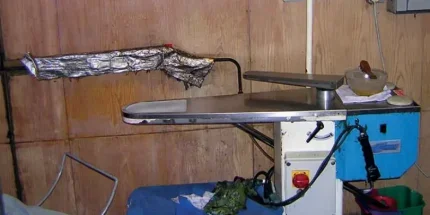
Experienced cleaners will know that, if a Biro or lipstick is missed during the pocket check, things can go badly wrong and really spoil your day; while other problems are just waiting around the corner to trip you up, like plastic buttons or beads that partially dissolve in solvent and mark off on items in the load. Then there are machine issues that can result in greying, cage marks or physical damage, not to mention the potential disasters due to colour loss/damage from spotting chemicals. Every cleaner sooner or later, either through an error of judgement, a manufacturing fault or even another cleaner’s mistake, can easily find themself facing a seriously expensive claim.
We suggest you cut out and keep this article for when you need it in the future!
Delicate fabrics
Delicate fabrics are at risk of physical damage throughout production, either from snagging on poorly maintained equipment, inadvertent exposure to spotting chemicals or from a classification error. Damage to silk fabrics is common in drycleaning but perhaps less so in wetcleaning. Silk has a high tensile strength, but is very sensitive to abrasion damage, causing what appears to be localised or random colour loss. The apparent colour loss is due to the ends of broken yarns projecting above the fabric causing differential light reflection from the surface and creating a cloudy ‘bloom’ effect.
Localised abrasion damage often occurs in a domestic environment, e.g. customers’ attempts at stain removal, and friction from car seat belts, shoulder bags and straps.
Inspection tip: damage will be most noticeable if you look horizontally across the fabric.
A frequent error in drycleaning is placing a silk item in a net bag, in the mistaken belief that bagging will protect it from damage in a ‘normal’ load of robust garments. This is poor cleaning practice and if items are damaged, the cleaner is responsible. However, mistakes do happen, and damage can often be recovered using the following procedure:
- Dissolve 200mls of liquid paraffin or suede & leather oil in 4.5 litres of solvent, or 1lt in 22.5 lt of solvent.
- Immerse the item in the solution; then give it a short spin in the cleaning machine.
- Tumble the item for 2 min. without heat or the fan; then dry at low temperature.
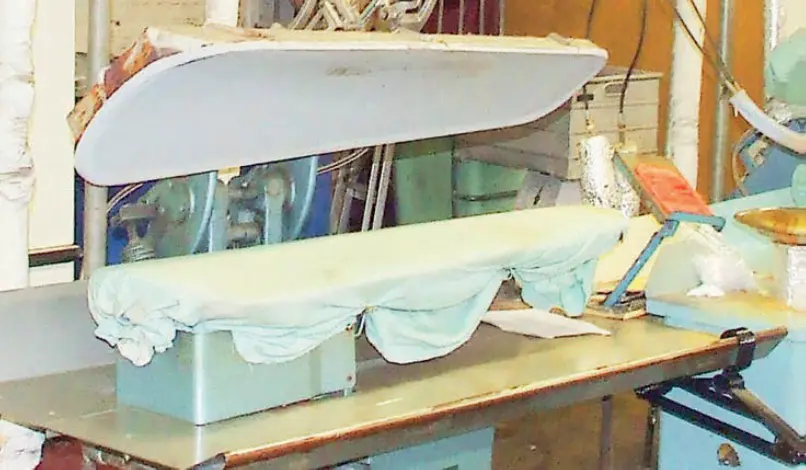
Emulsifiable oils are available from suppliers for treating washed/wetcleaned garments. These are also suitable for a drycleaned item if the care label allows a water-based process.
Abrasion damage spoils silk coat
Fault: The cleaner successfully cleaned this expensive silk coat in the past. On this occasion it was reportedly again cleaned on its own in perc in a net bag, but it came out of the machine with very severe abrasion damage. The care label was ℗ symbol. (Note: this garment (being pure silk) was wrongly labelled and should have carried the symbol.)
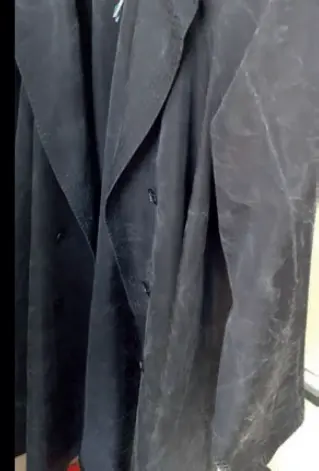
Technical cause: there are two possible explanations for the damage:
- The load processing conditions were not the same as on previous cleans, which resulted in the coat being exposed to excessive mechanical action during the drycleaning process. This is considered to be most unlikely as, even using a normal programme, cleaning the coat on its own in a net bag is unlikely to have resulted in such severe physical damage.
- When previously cleaned it was processed by another cleaner who had created the abrasion damage and then masked it using an oiling technique as described earlier; the oil then dissolved in this latest process. This leaves this cleaner ‘holding the baby’ for abrasion damage he is not responsible for. Under these circumstances there is unfortunately no way of determining who was actually responsible. However, it might be possible to recover the garment using the oiling technique described.
This is an interesting case which highlights the fact that although many expensive garments may be inadequately or – as in this case – wrongly labelled, a professional cleaner dealing with high value items should recognise this and select an appropriate cleaning programme designed for silk/delicate items.
Plastic beads dissolve!
A lucky escape – this beaded coat could have damaged every garment in the load. These beads passed the cleaner’s rub test with perc but dissolved in the cleaning cycle:
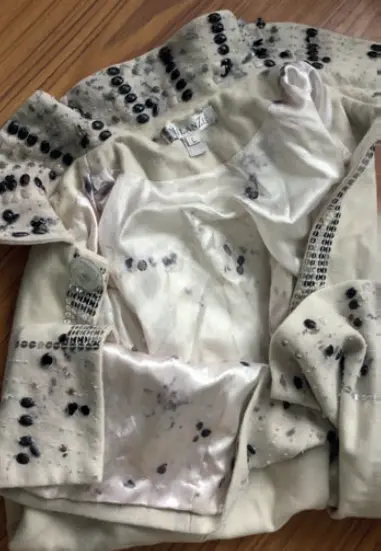
Fault: Before cleaning, the beads on this white coat were tested with perchloroethylene solvent and were found to be resistant. The heavily beaded coat was placed in a cleaning bag and then cleaned in a Normal Lights/White load. When removed from the machine, hundreds of beads were found contained in the bag and those still attached were badly affected and had marked off all over the coat. The instruction on the care label was ‘Dry Clean Only’! This was a lucky escape for the cleaner; were it not for the bag, many of the garments in the load could have been permanently stained, resulting in a huge bill for compensation.
Technical cause: this is one of those rare cases where checking the beads with solvent did not reveal they were partially soluble. This was almost certainly due to the longer time, higher solvent temperature and mechanical action to which the beads were exposed in cleaning and drying.
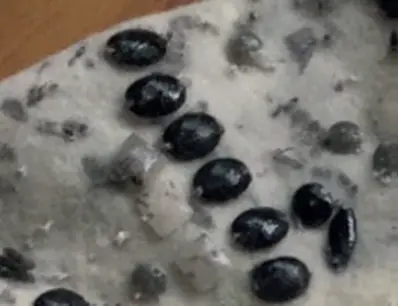
Responsibility: this was an expensive coat, and the cleaner took all reasonable precautions prior to cleaning. In view of its value and the inadequate aftercare label (it did not specify a solvent) and knowing full well the very high risks involving beaded items, the cleaner would have been wise to refuse it, or accept it at ‘owner’s risk’ and cleaned it using a less aggressive solvent. Having accepted it, the cleaner should negotiate sympathetically with the customer using the TSA Fair Compensation Guidelines.
Top Tip: instead of relying on a rub test with cotton fabric soaked in perc, remove one bead and leave it in perc for 30 min, then remove and squeeze between two pieces of cotton cloth.